
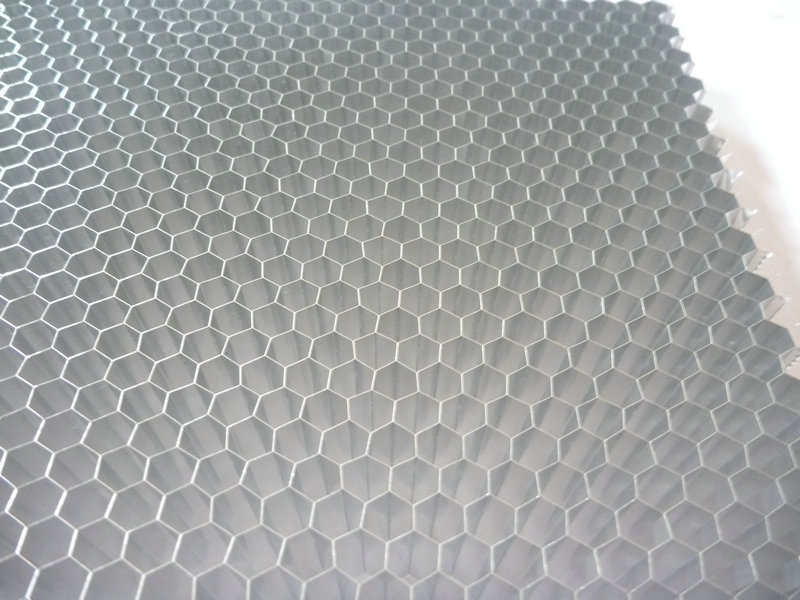
The experimental results suggest that as the impact velocity increases, the shape of the macroscopic yield surface changes, or more specifically, the curvature of the yield surface increases near the pure compression state. Based on the experimental results, a macroscopic yield criterion as a function of the impact velocity is proposed. The trends of the normalized normal crush strengths under inclined loads for specimens with different in-plane orientation angles as functions of the impact velocity are very similar to each other.

The results of the dynamic crush tests indicate that as the impact velocity increases, the normal crush more » strength increases and the shear strength remains nearly the same. The results of the quasi-static crush tests indicate that the normal crush and shear strengths under inclined loads are consistent with the corresponding results under combined loads. A test fixture was designed for both quasi-static and dynamic crush tests under inclined loads. Different types of honeycomb specimens were designed for crush tests under pure compressive and inclined loads with respect to the out-of-plane direction. The quasi-static and dynamic crush behaviors of aluminum 5052-H38 honeycomb specimens under out-of-plane inclined loads are investigated by experiments. Dynamic crush strength is determined from the weight of the impactor, height of the drop and difference in height of the honeycomb after the drop. The honeycomb structure will be on a rigid surface and the impactor will be dropped via a quick release hook. Dynamic impact testing will involve dropping a 43.8 lb impactor from a height around 5 feet onto the stainless steel honeycomb. This Instron machine uses a 20 ksi capacity load cell, while recording data at varying low strain rates. Compression testing to determine the static crush strength will use an Instron compression test machine. The material has a yield strength of 48 ksi and an ultimate strength of 103.2 ksi, with an elastic modulus of 29,300 ksi. The cell size of the material is 0.25 in and the ribbon thickness 0.003 in. The stainless steel honeycomb being tested will be cut into sections of about 2.0 inches in width, 2.3 inches in length and 2.5 inches in height. Both static and dynamic crush strengths of stainless steel honeycomb need to be quantified because strain rate more » plays a role in the material strength. Using a combination of the material properties and testing procedures both static and dynamic crush strength of stainless steel honeycomb will be determined.

Determines the viability of using 304 Stainless Steel honeycomb in future SRNL radioactive material packages. Mechanical properties of lightweight materials are well known compared to more dense materials like stainless steel. Their low density to high axial strength and inexpensive cost make them ideal for the energy absorption application. Honeycomb structures are used as energy absorbers to dissipate kinetic energy. Most of the experiments were conducted at an impact velocity of 11%. The honeycomb samples were crushed in all three orientations, W, L, and T. This report summarizes shock experiments with honeycomb densities of 22.1 pcf and 38.0 pcf and with crush weights of 45 lb, 168 lb, and 268 lb. This investigation also includes developing proper experimental methods for crush characterization, conducting discovery experiments to explore crush behaviors for model improvement, and identifying experimental and material uncertainties.Fifteen aluminum honeycomb cubes (3 in.) have been crushed in the Mechanical Shock Laboratory's drop table testing machines. Two sets of honeycombs were included in this investigation: commercial grade more » for initial exploratory experiments, and weapon grade, which satisfied B61 specifications. Volume I of this report documents an experimental study of the crush behavior of high-density honeycombs. In order to use honeycomb efficiently and to certify the payload is protected by the honeycomb under various loading conditions, a validated honeycomb crush model is required and the mechanical properties of the honeycombs need to be fully characterized. High-density aluminum honeycomb has been used in weapon assemblies to mitigate shock and protect payload because of its excellent crush properties. Honeycomb is a structure that consists of two-dimensional regular arrays of open cells.
